и других водородсодержащих газовых смесей при температуре среды до 200 град. С, - через 12 лет, при температуре среды свыше 200 град. С - через 8 лет;б) в производстве метанола: трубопроводы, предназначенные для транспортирования водородных газовых смесей, содержащих кроме водорода окись углерода, при температуре среды до 200 град. С, - через 12 лет, при температуре среды свыше 200 град. С - через 6 лет;в) в производстве капролактама: трубопроводы, предназначенные для транспортирования водородных газовых смесей при температуре среды до 200 град. С, - через 10 лет, трубопроводы, предназначенные для транспортирования окиси углерода при температуре свыше 150 град. С - через 8 лет;г) в производстве синтетических жирных спиртов (СЖС): трубопроводы, предназначенные для транспортирования водородных газовых смесей при температуре среды до 200 град. С, - через 10 лет, при температуре среды свыше 200 град. С - через 8 лет;трубопроводы, предназначенные для транспортирования пасты (катализатор с метиловыми эфирами) при температуре среды до 200 град. С, - через 3 года;д) в производстве мочевины: трубопроводы, предназначенные для транспортирования плава мочевины от колонны синтеза до дросселирующего вентиля, - через 1 год;трубопроводы, предназначенные для транспортирования аммиака от подогревателя до смесителя при температуре среды до 200 град. С, - через 12 лет;трубопроводы, предназначенные для транспортирования углекислого газа от компрессора до смесителя при температуре среды до 200 град. С, - через 6 лет;трубопроводы, предназначенные для транспортирования углеаммонийных солей (карбамата) при температуре среды до 200 град. С, - через 4 года.Генеральную выборочную ревизию трубопроводов, предназначенных для транспортирования других жидких и газообразных сред и других производств, следует также производить: при скорости коррозии до 0,1 мм/год и температуре до 200 град. С - через 10 лет;то же при температуре 200 - 400 град. С - через 8 лет;для сред со скоростью коррозии до 0,65 мм/год и температурой среды до 400 град. С - через 6 лет.При неудовлетворительных результатах генеральной выборочной ревизии назначается полная ревизия трубопровода.При полной ревизии разбирается весь трубопровод полностью, проверяется состояние узлов труб и деталей, а также арматуры, установленной на трубопроводе.Все трубопроводы и их участки, подвергавшиеся в процессе ревизии разборке, резке и сварке, после сборки подлежат испытанию на прочность и плотность.Для трубопроводов с Ру <= 10 МПа (100 кгс/см2) в обоснованных случаях при разборке фланцевых соединений, связанной с заменой прокладок, арматуры или отдельных элементов, допускается проводить испытания только на плотность. При этом вновь устанавливаемые арматуру или элементы трубопровода следует предварительно испытать на прочность пробным давлением.После проведения ревизии составляются акты, к которым прикладываются все протоколы и заключения о проведенных проверках.Результаты ревизии заносятся в паспорт трубопровода. Акты и остальные документы прикладываются к паспорту.После истечения проектного срока службы независимо от технического состояния трубопровод должен быть подвергнут комплексному обследованию (экспертизе промышленной безопасности) с целью установления возможности и сроков дальнейшей эксплуатации.Во время эксплуатации следует принять необходимые меры по организации постоянного и тщательного контроля за исправностью арматуры, а также за своевременным проведением ревизии и ремонта.При применении арматуры с сальниками особое внимание следует обращать на состояние набивочных материалов (качество, размеры, правильность укладки в сальниковую коробку).Асбестовая набивка, пропитанная жировым составом и прографиченная, может быть использована для рабочих температур не выше 200 град. С.Для температур выше 200 град. С и давлений до 25 МПа (250 кгс/см2) допускается применять прографиченную асбестовую набивку, если кольцо пересыпать слоем сухого чистого графита толщиной не менее 1 мм.Для высоких температур следует применять специальные набивки, в частности асбометаллические, пропитанные особыми составами, стойкими к разрушению и вытеканию под влиянием транспортируемой среды и высокой температуры.Для давлений свыше 32 МПа (320 кгс/см2) и температуры более 200 град. С следует применять специальные набивки.Сальниковые набивки арматуры следует изготавливать из плетеного шнура квадратного сечения со стороной, равной ширине сальниковой камеры. Из такого шнура на оправке следует нарезать заготовки колец со скошенными под углом 45 град. концами.Кольца набивки следует укладывать в сальниковую коробку, смещая линии разреза и уплотнение каждого кольца. Высоту сальниковой набивки следует принимать такой, чтобы грундбукса в начальном положении входила в сальниковую камеру не более чем на 1/6 - 1/7 ее высоты, но не менее чем на 5 мм.Сальники следует подтягивать равномерно без перекоса грундбуксы.Для обеспечения плотности сальникового уплотнения следует следить за чистотой поверхности шпинделя и штока арматуры.Прокладочный материал для уплотнения соединения крышки с корпусом арматуры следует выбирать с учетом химического воздействия на него транспортируемой среды, а также в зависимости от давления и температуры.Ход шпинделя в задвижках и вентилях должен быть плавным, а затвор при закрывании или открывании арматуры должен перемещаться без заедания.Предохранительные клапаны обслуживаются в соответствии с технической документацией и нормативно-технической документацией по промышленной безопасности.Не допускается применять добавочные рычаги при открывании и закрывании арматуры.Ревизию и ремонт трубопроводной арматуры, в том числе и обратных клапанов, а также приводных устройств арматуры (электро-, пневмо-, гидропривод, механический привод), как правило, производят в период ревизии трубопровода.Ревизию и ремонт арматуры следует производить в специализированных мастерских или ремонтных участках. В обоснованных допускается ревизия арматуры путем ее разборки и осмотра непосредственно на месте установки (приварная арматура, крупногабаритная, труднодоступная и т.д.).При ревизии арматуры, в том числе обратных клапанов, должны быть выполнены следующие работы:а) внешний осмотр;б) разборка и осмотр состояния отдельных деталей;в) осмотр внутренней поверхности и при необходимости контроль неразрушающими методами;г) притирка уплотнительных поверхностей (при необходимости);д) сборка, опробывание и опрессовка на прочность и плотность.При планировании сроков ревизии и ремонта арматуры следует в первую очередь проводить ревизию и ремонт арматуры, работающей в наиболее сложных условиях. Результаты ремонта и испытания арматуры оформляются актами и заносятся в эксплуатационную документацию.В случаях, когда характер и скорость коррозионного износа трубопровода не могут быть установлены типовыми методами контроля, используемыми при ревизии, для контроля приближения толщины стенки к отбраковочному размеру допускается выполнять контрольные засверловки.Трубопроводы, по которым транспортируются вещества группы А(а), А(б), газы всех групп, трубопроводы, работающие под вакуумом и высоким давлением [свыше 10 МПа (100 кгс/см2)], трубопроводы в блоках I категории взрывоопасности, а также трубопроводы, выполненные из аустенитных сталей и работающих в средах, вызывающих межкристаллитную коррозию, контрольным засверловкам не подвергают. В этих случаях следует установить контроль за состоянием толщины стенок трубопровода путем замера ультразвуковым толщиномером или иными допускаемыми методами.При засверловке контрольных отверстий следует пользоваться сверлом диаметром 2,5 - 5 мм, заправленным под острым углом, чтобы предотвратить большие утечки продукта.Отверстия при контрольных засверловках следует располагать в местах поворотов, сужений, врезок, застойных зонах, а также в тройниках, дренажных отводах, перед запорной арматурой и после нее и т.п. местах.Отверстия контрольных засверловок на отводах и полу отводах следует располагать преимущественно по наружному радиусу сгиба из расчета одно отверстие на 0,2 м длины, но не менее одного отверстия на отвод или секцию сварного отвода.Глубина контрольных засверловок устанавливается равной расчетной толщине трубопровода плюс П х С (где П - половина периода между очередными ревизиями, год, С - фактическая скорость коррозии трубопровода, мм/год).Места расположения контрольных засверловок на трубопроводе следует четко обозначить и зафиксировать в документации.Пропуск контрольного отверстия на трубопроводе свидетельствует о приближении толщины стенки к отбраковочному размеру, поэтому такой трубопровод следует подвергнуть внеочередной ревизии.Периодические испытания трубопроводов на прочность и плотность проводят, как правило, во время проведения ревизии трубопровода.Сроки проведения испытания для трубопроводов с давлением до 10 МПа (100 кгс/см2) принимается равным удвоенной периодичности проведения ревизии, принятой согласно требованиям п. 9.3.3 для данного трубопровода, но не реже одного раза в 8 лет.Сроки проведения испытания для трубопроводов с давлением свыше 10 МПа (100 кгс/см2) должны быть не реже: для трубопроводов с температурой до 200 град. С - один раз в 8 лет;для трубопроводов с температурой свыше 200 град. С - один раз в 4 года.Испытательное давление и порядок проведения испытания должны соответствовать требованиям раздела 8 настоящих Правил.При проведении испытания на прочность и плотность допускается применение акустико-эмиссионного контроля.Результаты периодических испытаний трубопроводов оформляются в установленном порядке.Трубы, детали трубопроводов, арматура, в том числе литая (корпуса задвижек, вентили, клапаны и т.п.), подлежат отбраковке: · если в результате ревизии окажется, что из-за воздействия среды толщина стенки стала ниже проектной и достигла величины, определяемой расчетом на прочность без учета прибавки на коррозию (от браковочный размер);· От браковочные толщины стенок элементов трубопровода следует указывать в проектной документации. Трубы и детали трубопроводов отбраковываются, если: · при ревизии на поверхности были обнаружены трещины, отслоения, деформации (гофры, вмятины, вздутия и т.п.);· в результате воздействия среды за время работы до очередной ревизии толщина стенки выйдет за пределы от браковочных размеров, определяемых расчетом на прочность;· изменились механические свойства металла;· при контроле сварных швов обнаружены дефекты, не подлежащие исправлению;· размеры резьбовых соединений вышли из поля допусков или на резьбе имеются срывы витков, трещины, коррозионный износ;· трубопровод не выдержал гидравлического или пневматического испытаний;· уплотнительные элементы арматуры износились так, что не обеспечивают безопасное ведение технологического процесса.Фланцы отбраковываются при: неудовлетворительном состоянии привалочных поверхностей;· наличии трещин, раковин и других дефектов;· деформации;· уменьшении толщины стенки воротника фланца до от браковочных размеров трубы;· срыве, смятии и износе резьбы в резьбовых фланцах высокого давления, а также при наличии люфта в резьбе, превышающего допустимые пределы. Линзы и прокладки овального сечения отбраковываются при наличии трещин, забоин, сколов, смятии уплотнительных поверхностей, деформации.Крепежные детали отбраковываются: · при появлении трещин, срыва или коррозионного износа резьбы;· в случаях изгиба болтов и шпилек;· при остаточной деформации, приводящей к изменению профиля резьбы;· в случае износа боковых граней головок болтов и гаек;· в случае снижения механических свойств металла ниже допустимого уровня.Сильфонные и линзовые компенсаторы отбраковываются в следующих случаях:· толщина стенки сильфона или линзы достигла расчетной величины,указанной в паспорте компенсатора;· толщина стенки сильфона достигла 0,5 мм, а расчетная толщина стенки сильфона имеет более низкие значения;· при наработке компенсаторами допустимого числа циклов с учетом условий эксплуатации на пожароопасных и токсичных средах.Нормы отбраковки следует указывать в ремонтной документации с учетом условий конкретного объекта.
3 Техническое обслуживание и ремонт оборудования
3.1 Техническое обслуживание оборудования
Техническое состояние технологических трубопроводов газоперекачивающих компрессорных станций (КС) с увеличением сроков их эксплуатации, требует разработки системы специальных мероприятий по обеспечению заданного уровня надежности, так как эксплуатация за пределами расчетного ресурса сопровождается повышением вероятности аварий, в том числе и с тяжелыми экологическими последствиями. В настоящее время, внедрение инновационных средств технической диагностики позволило заменить традиционную систему эксплуатации с регламентным ремонтно-техническим обслуживанием - на эксплуатацию по техническому состоянию, т.е. к обслуживанию в зависимости от степени риска, от реального состояния и фактических характеристик объектов. Для выполнения существующих повышенных требований к экологической и технической безопасности – требуется развитие и внедрение единой системы экспертно-диагностического обслуживания (ЭДО) трубопроводов, являющейся важным инструментом реализации стратегии эффективного управления основных фондов.
Цель функционирования системы ЭДО - обеспечение надежности объектов на заданном уровне, при оптимальном вложении финансовых средств на их эксплуатацию (рис.1).
Задачи системы ЭДО приведены в табл.1.

Рис.1. Стратегия управления основными фондами
Таблица 1. Задачи экспертно-диагностического обслуживания трубопроводов.
№ п/п
|
Задача
|
Метод решения
|
Средства выполнения
|
Ожидаемый результат
|
1 |
Обоснование краткосрочных, среднесрочных, долгосрочных планов ремонта |
Ранжирование участков трубопроводов по степени опасности |
Комплексная аналитическая база данных различных обследований, ремонта, реальных условий эксплуатации |
Обеспечение темпов проведения ремонтно-восстановительных работ не ниже темпов роста количества опасных дефектов |
Периодический мониторинг потенциально-опасных участков трубопровода |
2 |
Оптимизация технологического процесса проведения ремонтно-восстановительных работ (РВР) |
Принятие технически и экономически обоснованных методов и средств ремонта |
Разработка Регламента проведения РВР |
«Прозрачность» расходов, снижение затрат по ремонту на 20…30% |
Повторное применение и ремонт труб, соединительных деталей |
Методика оценки степени пригодности труб и деталей, цеха по ремонту и изоляции |
Отсутствие простоев ремонтных бригад за счет создания резерва МТР, снижение затрат по закупке материалов на 30…40% |
3 |
Подготовка методической базы для создания эффективных отраслевых руководящих документов |
Осуществление "обратной связи" отраслевой науки с производством, промышленная апробация новых технологий |
Полигонные испытания дефектных деталей с действующих объектов трубопровода |
Совершенствование методов диагностики; реальная оценка технического состояния трубопроводов |
Нивелирование противоречивости и консервативности действующей нормативно-технической документации |
Разработка и внедрение региональных стандартов предприятий с учетом местных условий и требований |
Четкая система ведения работ, диверсификация ответственности руководителей предприятий, эксплуатирующих трубопроводы |
СТРУКТУРА ЭКСПЕРТНО-ДИАГНОСТИЧЕСКОГО
ОБСЛУЖИВАНИЯ
Принципиальным положением в ЭДО является концепция
технического
обслуживания и ремонта
оборудования и
трубопроводов по фактическому состоянию на основе диагностики. Это позволит обеспечить возможность обоснованного планирования
технического
обслуживания и ремонтов по объемам и срокам, что приведет к снижению эксплуатационных затрат за счет уменьшения
обслуживаний и числа отказов.
Основные элементы экспертно-диагностического
обслуживания (Рис.2 – Структура ЭДО
трубопроводов):
· Контроль
технического состояния – оценка
технического состояния технологических
трубопроводов и
оборудования и сопоставление фактических параметров с проектными параметрами;
· Техническое
обслуживание – работы по поддержанию работоспособного и исправного состояния технологических
трубопроводов и
оборудования в процессе эксплуатации;
· Ремонт – комплекс операций по восстановлению исправного и работоспособного состояния технологических трубопроводов и оборудования;
· Замена оборудования – работы связанные с выводом из эксплуатации, демонтажем, ликвидацией оборудования и заменой его на новое оборудование.
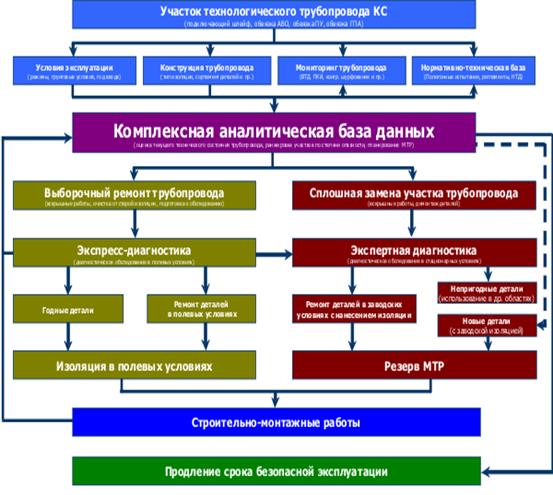
Рис.2 – Структура ЭДО технологических трубопроводов КС.
3.2 Подготовка к ремонту оборудования
Образование взрывоопасной смеси хлора с водородом, приводящей к взрывам и разрушениям сосудов и трубопроводов, содержащих жидкий и газообразный хлор;
Большое значение для безопасной эксплуатации производства имеет правильная организация ремонта и тщательная подготовка аппаратов и трубопроводов к ремонтным работам. Отложения полимеров ацетиленовых углеводородов и ацетилен, сортируемый продуктами коррозии, с трудом и очень медленно удаляются при продувках. Известны случаи взрыва ацетилена при сварочных работах даже в тщательно продутых трубопроводах. Подготовка к ремонту аппаратов и трубопроводов, содержащих ацетилен, должна состоять в продувке их азотом для удаления основного количества С2Н2. длительной пропарке и повторной продувке азотом. Во избежание возможности полимеризации (при высоких температурах) высших ацетиленовых углеводородов, содержащихся в газе, рекомендуется до продувки паром продуть аппаратуру и коммуникации азотом до отсутствия горючих компонентов в продувочном газе.
-с разборкой аппаратуры, оборудования и трубопроводов, содержащих горючие и легковоспламеняющиеся вещества;
-с разборкой аппаратуры, оборудования и трубопроводов, содержащих горючие и легковоспламеняющиеся вещества;
Надежность работы предохранительного клапана обеспечиваете правильным расчетом его пропускной способности, точной регулировкой пружины и затвора и контролем за исправностью действия. Пропускная способность клапана (в кг/ч) рассчитывается по формуле, приведенной в «Правилах по сосуд г м», регулировка пружины на установочное давление и затора на герметичность проводится на специальном стенде, кон"роль осуществляется посредством устройства для принудительного пробного открытия клапана (подрыва) в процессе его эксплуатации. Для сосудов, аппаратов, трубопроводов, содержащих некоторые ядовитые, горючие и взрывоопасные среды, допускается установка предохранительных клапанов без устройств для подрыва, при условии, что клапаны будут подвергаться ревизии в сроки, определенные «Правилами по сосудам».
В воздушных компрессорах возможно образование взрывоопасных смесей даже при небольших количествах горючих газов, уступающих с забираемым воздухом. Поэтому воздух забирают из зоны, не содержащей примесей горючих газов и пыли, а высоте не менее 2—3 м от уровня земли и очищают в фильтрах различной конструкции (например, состоящих из пластин, пропитанных висциновым маслом или из специальных волокон). Во избежание попадания в трубопроводы сжатого BosAvxa взрывоопасных или токсичных веществ правилами запрещается устройство постоянных врезок от трубопроводов, содержащих такие вещества. Система снабжения сжатым воздухом должна обладать повышенной надежностью, поскольку прекращение его подачи для КИП и автоматики делает технологические установки неуправляемыми. Чтобы предотвратить серьезные аварии предусматривается 100%-ное резервирование компрессоров, подающих воздух для систем КИП и автоматика.
Для трубопроводов, содержащих хлор, необходимо предусматривать возможность их опорожнения путем продувки сухим (с точкой росы минус 40 °С) сжатым воздухом (азотом) или вакуумированием с последующей продувкой сухим сжатым воздухом (азотом) до остаточной концентрации хлора в газах продувки не более 1 мг/м3.
Во избежание самовозгорания омега-полимера, во всех случаях остановки аппаратов или трубопроводов, содержащих этот полимер, они должны обильно орошаться водой до выгрузки и освобождения их от продукта.
Сквозной проход через ЭМП трубопроводов, содержащих взрывоопасные газы, горючие или легковоспламеняющиеся жидкости, не допускается. В ЭМП разрешается прокладывать только трубопроводы, непосредственно относящиеся к установленному в них обору- сжатия этих газов до необходимого давления допускается на обоснованное использование воздуха (окислителя) для испытания на плотность технологических систем перед заполнение: их горючими газами и жидкостями, пары которых образуют воздухом взрывоопасные смеси. В ряде производств вмести инертного газа используется воздух для продувки аппаратов трубопроводов, содержащих взрывоопасные газы и пары; на всегда производится продувка инертным газом аппаратуры перед заполнением ее ЛВЖ и горючими газами, или она проводится недостаточным количеством инертного газа, что не обеспечивает необходимое удаление воздуха. Надежность работы предохранительного клапана обеспечивается правильным расчетом его пропускной способности, точной регулировкой пружины и затвора
29-04-2015, 00:56