Невероятный труд, изобретательность и внимание потребовались литейщикам для того, чтобы избежать в таких крайне неблагоприятных условиях спекания (сплавления) металла отливки с материалом формы. Даже в обычных отливках жидкий металл проникает в поры формы, сплавляется с ее материалом, что приводит к полной негодности отливки. В форме же Царь-отливки давление жидкого металла в десятки раз превышало давление в обычных отливках. Кроме того, если залитый в обычную форму металл пребывает в жидком состоянии в течение нескольких минут, а затем затвердевает, то в форме Царь-отливки он находился в жидком состоянии, то есть в состоянии наиболее активного воздействия на стенки формы, в течение десятков часов.
У литейщиков, отливавших мотовилихинский шабот, не было забот, которые бы не вырастали в проблемы, беспрецедентные в их решении: все было ново, трудно, необычно, без дорог, проторенных на других заводах, в других странах.
Огромные трудности возникли при одной из заключительных операций литья — заливке формы. Литейщики считают заливку хоть и ответственной, но самой простой операцией литья. Заливка же шабота превратилась в почти непреодолимую трудность. Где взять сразу почти 650 т чугуна? Такое количество чугуна — почти суточная выплавка крупной доменной печи того времени. Но доменной печи на Мотовили-хинском заводе не было. Русские литейщики предлагают дерзкий, никем не повторенный план: построить возле формы специальный металлургический цех. Огромный литейный цех для одной заливки! И такой цех был построен. По мощности мало какие современные цехи могут с ним стать в ряд. Литейщики Мотовилихи построили специально вокруг формы двадцать крупных вагранок. Целые сутки потребовалось литейщикам, чтобы вывести эти вагранки «на старт», то есть привести их все одновременно в рабочее состояние. А затем уже началась плавка металла. Вагранки с учетом периода наладки работали непрерывно в течение 120 ч. Металл многие десятки часов непрерывно лился из леток вагранок по каналам прямо в форму. Такого еще мир никогда не знал, это никому не удалось повторить. Заливка формы была завершена благополучно.
Началось остывание металла. Через месяц в форме просверлили дыру и замерили температуру поверхности отливки: она составила почти 700° С. В течение почти трех месяцев тепло отливки использовали медники, паяльщики и другие рабочие для расплавления олова, припоев и т. п. Только через три месяца с момента заливки колоссальный шабот в 630 т вынули из формы, передвинули, перевернули и установили на месте расположения молота без подъемных кранов, с помощью одних рычагов и блоков. Беспредельны возможности ума и рук человеческих!
ЛИТОЙ ПАРОВОЗ
Вес литых деталей в общем балансе всех металлических заготовок для современных машин составляет около 50%. На долю заготовок, полученных всеми прочими способами (сваркой, штамповкой, прокаткой и т. п.), приходится остальная часть веса машин. Такое преимущественное положение литья объясняется рядом его достоинств, одно из которых состоит в том, что литьем можно получить детали практически любых габаритных размеров, веса и конфигурации.
|
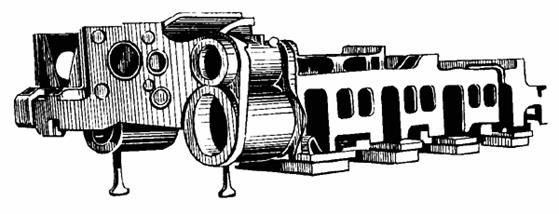
Эти преимущества литья широко используются конструкторами. При переходе к литым заготовкам они в одной сложной отливке совмещают большое количество деталей, получаемых любым другим способом. Правда, это усложняет работу литейщиков, но приносит огромную экономию предприятию в целом. Возможности совмещения в одной литой конструкции большого количества отдельных деталей практически не ограничены.
Примером объединения большого количества кованых деталей в одной отливке может быть паровозная рама с цилиндрами (рис. 3). Обычно многие узлы ее представляют самостоятельные отливки, поковки или детали, изготовленные из проката. Такая же отливка включает в себе два паровозных цилиндра, раму паровоза и другие детали, отлитые заодно, словом, чуть не весь паровоз. Отливка получилась не только крупной, но и чрезвычайно сложной. Ее общая длина почти 15 м, ширина около 3 м, общий вес около 7 т. Изготовление литой паровозной рамы было связано с чрезвычайно большими трудностями: понадобилась новая сложная оснастка (опоки и др.), возникла необходимость в специальных мерах предупреждения трещин в отливках и т. д. Но зато значительно снизилась трудоемкость механической обработки и сборки машины. И хотя литейщикам пришлось решить трудную технологическую задачу, они с ней справились хорошо — ими была создана уникальная в своем роде отливка.
При изучении такой сложной отливки возникают вопросы: насколько целесообразно изготовление подобных отливок? Где должна быть граница объединения отдельных простых деталей в сложную литую? На эти вопросы можно ответить правильно лишь на основе глубокого экономического анализа каждого случая, на основе учета общих затрат как на подготовительные, так и последующие после процесса литья операции.
Для современного литейного производства случаи создания огромных и весьма ответственных отливок нередки. Отливки для турбин мощных гидростанций, крупных компрессоров и прокатных станов, отливки из новых сплавов с особыми свойствами, способными удовлетворять требованиям работы в тяжелых условиях (при больших давлениях, весьма низких температурах и т.п.), отливки чрезвычайной сложности и повышенной точности требуют каждый раз особых решений, больших научных поисков, часто становятся выдающимися произведениями искусства литья.
29-04-2015, 04:18