Толщина фланца корпуса b=1,5= 12 мм.
Толщина фланца крышки корпуса b1=1,51= 10,5 мм.
Толщина нижнего пояса корпуса p=2,35= 19 мм.
Толщина ребер основания корпуса m=(0,85...1)= 8 мм.
Толщина ребер крышки m1=(0,85...1)1= 7 мм.
Диаметр болтов:
соединяющих основание корпуса с крышкой d=32Тт= 12 мм.
у подшипников d1=(0,7...0,75)d= 10 мм.
фундаментных болтов dф=1,25d= 16 мм.
Размеры, определяющие положение болтов d2:
е=(1...1,2)d1= 11 мм.
q=0,5d2+d4= 17 мм.
Дополнительные элементы корпуса.
Гнездо под подшипник:
диаметр отверстия в гнезде под быстроходный вал Dп1= 100 мм.
диаметр отверстия в гнезде под тихоходный вал Dп2= 100 мм.
винты крепления крышки подшипника быстроходного вала М 12
винты крепления крышки подшипника тихоходного вала М 12
число винтов крышки подшипника быстроходного вала n1= 6
минимальное число винтов крышки подшипника тихоходного вала n2= 6
диаметр гнезда под подшипник быстроходного вала Dк1=D1+3= 154 мм.
диаметр гнезда под подшипник тихоходного вала Dк2=D2+3= 154 мм.
длина гнезда l=d+c2+Rб+(3...5)= 36 мм.
Радиус Rб= 11 мм.
Расстояние до стенки корпуса с2=Rб+2= 13 мм.
Размеры штифта по ГОСТ 3129-70 (табл10.5. [3]):
dш= 12 мм.
lш=b+b1+5= 30 мм.
Предусмотрим уклон днища 2° в сторону маслоспускного отверстия для облегчения слива масла. Для заливки масла и осмотра в крышке корпуса выполним окно, закрываемое крышкой.
10.4. Установка элементов передач на вал.
Для соединения вала с элементами открытой передачи используем шпоночное соединение, при нереверсивной работе без толчков и ударов применяем посадку Н7/k6.
Для установки полумуфты на вал назначаем посадку- Н7/k6.
При передаче вращающего момента шпоночным соединением для цилиндрических колес назначаем посадку Н7/r6.
Посадка призматической шпонки по ГОСТ 23360-78 по ширине шпонки p9, по ширине шпоночного паза P9.
Посадка подшипников на вал k6, поле допуска отверстия для наружного кольца подшипников-Н7.
СМАЗЫВАНИЕ.
С целью защиты от коррозии и снижения коэффициента трения, уменьшения износа, отвода тепла и продуктов износа от трущихся поверхностей, снижения шума и вибрации применяют смазывание зацеплений и подшипников.
а) Смазывание зацепления.
Применяем непрерывное смазывание жидким маслом окунанием.
В зависимости от контактного напряжения и окружной скорости выбираем по табл. 10.29. [1] следующий сорт масла: И-Т-Д-100
Количество масла принимаем, из расчета 0,4...0,8 литра на 1кВт. Мощности, равным 3,2 л.
б) Для контроля уровня масла, находящегося в редукторе, предусматриваем оконный маслоуказатель.
в) Для слива масла, налитого в корпус редуктора, предусматриваем в корпусе сливное отверстие, закрываемое пробкой с цилиндрической резьбой.
г) При длительной работе, в связи с нагревом масла и воздуха повышается давление внутри корпуса, что приводит к просачиванию масла через уплотнения и стыки.
Чтобы избежать этого, предусматриваем отдушину, связывающую внутреннюю полость редуктора с внешней средой.
ПРОВЕРОЧНЫЕ РАСЧЁТЫ.
Проверочный расчёт подшипников
Быстроходный вал.
Входные данные:
Угловая скорость вала = 50,79 с-1.
Осевая сила Fa= 5180,125 Н.
Реакции в подшипниках:
В правом R1= 1723,592 Н.
Влевом R2= 1683,515 Н.
Характеристика подшипников:
Рядность подшипников в наиболее нагруженной опоре i= 1
Базовая грузоподъемность CR= 50500 Н.
Статическая грузоподъёмность C0r= 41000 Н.
Коэффициент радиальной нагрузки X= 0,45
Отношение iRF/(C0R)= 0,12634451
Коэффициент осевой нагрузки Y= 1,13
Коэффициент влияния осевого нагружения е= 0,48 кН.
Осевая составляющая радиальной нагрузки подшипника RS1= 827,3 Н.
Осевая составляющая радиальной нагрузки подшипника RS2= 808,1 Н.
Осевая нагрузка подшипника RА1= 827,3 Н.
Осевая нагрузка подшипника RА2= 6007,4 Н.
Радиальная нагрузка подшипника Rr= 1723,6 Н.
Коэффициент безопасности Кб= 1,1
Температурный коэффициент К= 1
Коэффициент вращения V= 1
Расчёт:
Отношение RA/(V*Rr)= 3,485
Эквивалентная динамическая нагрузка RE=(XVRr+YRa)KбKт= 8320,38
По ГОСТ 16162-85 для червячных редукторов принимаем Lh=5000 часов.
Для шариковых подшипников показатель степени: m=3
Определяем расчётную динамическую грузоподъёмность
Crp=RE*m573Lh/106= 43763,37 Н.
Подшипник пригоден
Долговечность подшипника L10h=106*(Cr/RE)m/(573)= 7682,7 часов.
Тихоходный вал.
Входные данные:
Угловая скорость вала = 6,35 с-1.
Осевая сила Fa= 2684 Н.
Реакции в подшипниках:
В правом R1= 7181,083 Н.
Влевом R2= 6997,609 Н.
Характеристика подшипников:
Рядность подшипников в наиболее нагруженной опоре i= 1
Базовая грузоподъемность CR= 30700 Н.
Статическая грузоподъёмность C0r= 19600 Н.
Коэффициент радиальной нагрузки X= 0,56
Отношение iRF/(C0R)= 0,13693878
Коэффициент осевой нагрузки Y= 1,286
Коэффициент влияния осевого нагружения е= 0,34 кН.
Осевая составляющая радиальной нагрузки подшипника RS1= 0 Н.
Осевая составляющая радиальной нагрузки подшипника RS2= 0 Н.
Осевая нагрузка подшипника RА1= 2684 Н.
Осевая нагрузка подшипника RА2= 2684 Н.
Радиальная нагрузка подшипника Rr= 7181,083 Н.
Коэффициент безопасности Кб= 1,1
Температурный коэффициент К= 1
Коэффициент вращения V= 1
Расчёт:
Отношение RA/(V*Rr)= 0,37375978
Эквивалентная динамическая нагрузка RE=(XVRr+YRa)KбKт= 8220,33353
По ГОСТ 16162-85 для червячных редукторов принимаем Lh=5000 часов.
Для шариковых подшипников показатель степени: m=3
Определяем расчётную динамическую грузоподъёмность Crp=RE*m573Lh/106= 21619,9933 Н.
Подшипник пригоден
Долговечность подшипника L10h=106*(Cr/RE)m/(573)= 14315,8936 часов.
Проверочный расчёт шпонок.
Проверку шпонок ведём на смятие. Про допустимом напряжении []см= 150 Н/мм2.
Шпонка на выходном конце быстроходного вала .
Диаметр вала d= 38 мм.
Из конструктивной компоновки полная длинна шпонки l= 45 мм.
По табл. К42. [1] определяем:
ширина шпонки b= 10 мм.
высота шпонки h= 8 мм.
глубина паза вала t1= 5 мм.
Определяем рабочую длину шпонки lр=l-b= 35 мм.
Определяем площадь смятая Асм=(0,94*h-t1)*lp= 88,2 мм2.
Окружная сила на быстроходном валу Ft= 2684,000 Н.
Расчётная прочность см=Ft/Aсм= 88,2 < 150 (Н/мм2)
Условие прочности см < см выполнено.
Шпонка вала под колесо.
Из проектного расчета вала принимаем диаметр вала под зубчатым колесом d= 75 мм.
Из конструктивной компоновки полная длинна шпонки l= 120 мм.
По табл. К42. [1] определяем:
ширина шпонки b= 20 мм.
высота шпонки h= 12 мм.
глубина паза вала t1= 7,5 мм.
Определяем рабочую длину шпонки lр=l-b= 100 мм.
Определяем площадь смятая Асм=(0,94*h-t1)*lp= 378 мм2.
Окружная сила на колесе Ft= 7487,3 Н.
Расчётная прочность см=Ft/Aсм= 19,81 < 150 (Н/мм2)
Условие прочности см < см выполнено.
Шпонка на выходном конце тихоходного вала .
Из проектного расчета вала принимаем диаметр выходного конца вала d= 60 мм.
Из конструктивной компоновки полная длинна шпонки l= 71 мм.
По табл. К42. [1] определяем:
ширина шпонки b= 16 мм.
высота шпонки h= 10 мм.
глубина паза вала t1= 6 мм.
Определяем рабочую длину шпонки lр=l-b= 55 мм.
Определяем площадь смятая Асм=(0,94*h-t1)*lp= 187 мм2.
Окружная сила на тихоходном валу Ft= 5180,1 Н.
Расчётная прочность см=Ft/Aсм= 27,701 < 150 (Н/мм2)
Условие прочности см < см выполнено.
Уточненный расчет валов [3].
Примем, что нормальные напряжения от изгиба изменяются по симметричному циклу, а касательные от кручения по отнулевому. Расчет производим для предположительно опасных сечений каждого из валов.
Быстроходный вал.
Проедал выносливости при симметричном цикле изгиба
Предел на растяжение B= 900,00 H/мм2.
-1=0,43в= 387,00 H/мм2.
Проедал выносливости при симметричном цикле касательных напряжений
-1=0,58-1= 224,46 H/мм2.
Сечение А-А.
Это сечение под элементом открытой передачи рассчитываем на кручение. Концентрацию напряжений вызывает наличие шпоночной канавки.
Определяем коэффициент запаса прочности по касательным напряжениям.
Диаметр выходного конца вала d= 38 мм.
Для этого находим:
среднее напряжение отнулевого цикла Wк нетто=d3/16-bt1(d-t1)2/2d= 10057,64 мм3
амплитуда отнулевого цикла v=m=max/2=T1/2Wк нетто= 5,34 H/мм2.
принимаем по табл. 8.5. , 8.8 , эффективный коэффициент концентрации касательных напряжений k= 1,9
интерполируя, масштабный фактор для касательных напряжений = 0,738
коэффициент = 0,1
коэффициент, учитывающий влияние шероховатости поверхности = 0,95
Коэффициент запаса прочности s=-1/(k*v/(*)+*m)= 14,96
Определяем коэффициент запаса прочности по нормальным напряжениям .
Для этого находим:
момент консольной нагрузки М= Fоп*lоп= 110213 H*мм.
среднее напряжение отнулевого цикла Wк нетто=d3/32-bt1(d-t1)2/2d= 4670,60 мм3.
амплитуда отнулевого цикла v=m=max/2=T1/2Wк нетто= 22,99 H/мм2.
принимаем по табл. 8.5. , 8.8, эффективный коэффициент концентрации касательных напряжений k= 1,9
интерполируя, масштабный фактор для нормальных напряжений = 0,856
коэффициент = 0,2
коэффициент, учитывающий влияние шероховатости поверхности = 0,95
Коэффициент запаса прочности s=-1/(k*v/(*)+*m)= 6,637
Результирующий коэффициент запаса прочности для сечения А-А
s=s*s*/s2+s2= 6,067
Сечение Б-Б.
Это сечение под подшипником. Концентрация напряжений вызывает посадка подшипника с гарантированным натягом.
Определяем коэффициент запаса прочности по касательным напряжениям.
Диаметр вала под подшипник d= 45 мм.
Отношение D/d= 1,24
Выбираем радиус галтели r= 1,00 мм.
Отношение r/d= 0,02
Определяем коэффициент запаса прочности по касательным напряжениям.
Для этого находим:
Изгибающий момент M=Fвl3= 110213 H*мм.
осевой момент сопротивления W=d3/32= 8946,18 мм3
полярный момент Wp=2W= 17892,36 мм3
амплитуда и среднее напряжение цикла костыльных напряжений
v=m=max/2=T1/2Wp= 3,00 H/мм2.
принимаем по табл. 8.5. , 8.8 , эффективный коэффициент концентрации касательных напряжений k= 1,9
масштабный фактор для касательных напряжений = 0,715
коэффициент = 0,1
коэффициент, учитывающий влияние шероховатости поверхности = 0,95
Коэффициент запаса прочности s=-1/(k*v /(*)+*m)= 25,825
Определяем коэффициент запаса прочности по нормальным напряжениям .
Для этого находим:
амплитуда нормальных напряжений v=m=max/2=М/2W= 6,16 H/мм2.
принимаем по табл. 8.5. , 8.8, эффективный коэффициент концентрации касательных напряжений k= 2,8
масштабный фактор для касательных напряжений = 0,835
коэффициент = 0,2
коэффициент, учитывающий влияние шероховатости поверхности = 0,95
Коэффициент запаса прочности s=-1/(k*v /(*)+*m)= 16,844
Результирующий коэффициент запаса прочности для сечения Б-Б
s=s*s*/s2+s2= 14,108
Тихоходный вал.
Проедал выносливости при симметричном цикле изгиба
Предел на растяжение B= 900 H/мм2.
-1=0,43в= 387 H/мм2.
Предал выносливости при симметричном цикле касательных напряжений
-1=0,58-1= 224,46 H/мм2.
Сечение А-А.
Это сечение под элементом открытой передачи рассчитываем на кручение. Концентрацию напряжений вызывает наличие шпоночной канавки.
Определяем коэффициент запаса прочности по касательным напряжениям.
Диаметр выходного конца вала d= 60 мм.
Для этого находим:
среднее напряжение отнулевого цикла Wк нетто=d3/16-bt1(d-t1)2/2d= 40078,70 мм3
амплитуда отнулевого цикла v=m=max/2=T2/2Wк нетто= 10,34 H/мм2.
принимаем по табл. 8.5. , 8.8 , эффективный коэффициент концентрации касательных напряжений k= 1,9
интерполируя, масштабный фактор для касательных напряжений = 0,675
коэффициент = 0,1
коэффициент, учитывающий влияние шероховатости поверхности = 0,95
Коэффициент запаса прочности s=-1/(k*v /(*)+*m)= 7,087
Определяем коэффициент запаса прочности по нормальным напряжениям .
Для этого находим:
момент консольной нагрузки М= Fоп*lоп= 848571 H*мм.
среднее напряжение отнулевого цикла Wк нетто=d3/32-bt1(d-t1)2/2d= 18872,95 мм3.
амплитуда отнулевого цикла v=m=max/2=T2/2Wк нетто= 43,92 H/мм2.
принимаем по табл. 8.5. , 8.8, эффективный коэффициент концентрации касательных напряжений k= 1,9
интерполируя, масштабный фактор для нормальных напряжений = 0,79
коэффициент = 0,2
коэффициент, учитывающий влияние шероховатости поверхности = 0,95
Коэффициент запаса прочности s=-1/(k*v /(*)+*m)= 3,226
Результирующий коэффициент запаса прочности для сечения А-А
s=s*s*/s2+s2= 2,936
Сечение Б-Б.
Это сечение под подшипником. Концентрация напряжений вызывает посадка подшипника с гарантированным натягом.
Диаметр вала под подшипник d= 65 мм.
Отношение D/d= 1,15
Выбираем радиус галтели r= 1,50 мм.
Отношение r/d= 0,02
Определяем коэффициент запаса прочности по касательным напряжениям.
Для этого находим:
Изгибающий момент M=Fвl3= 614 H*мм.
осевой момент сопротивления W=d3/32= 26961,25 мм3
полярный момент Wp=2W= 53922,50 мм3
амплитуда и среднее напряжение цикла костыльных напряжений
v=m=max/2=T1/2Wp= 7,69 H/мм2.
принимаем по табл. 8.5. , 8.8 , эффективный коэффициент концентрации касательных напряжений k= 1,67
масштабный фактор для касательных напряжений = 0,6625
коэффициент = 0,1
коэффициент, учитывающий влияние шероховатости поверхности = 0,95
Коэффициент запаса прочности s=-1/(k*v /(*)+*m)= 10,601
Определяем коэффициент запаса прочности по нормальным напряжениям .
Для этого находим:
амплитуда нормальных напряжений v=m=max/2=М/2W= 0,01 H/мм2.
принимаем по табл. 8.5. , 8.8, эффективный коэффициент концентрации касательных напряжений k= 2,68
масштабный фактор для касательных напряжений = 0,775
коэффициент = 0,2
коэффициент, учитывающий влияние шероховатости поверхности = 0,95
Коэффициент запаса прочности s=-1/(k*v /(*)+*m)= 10077,947
Результирующий коэффициент запаса прочности для сечения Б-Б
s=s*s*/s2+s2= 10,601
Сечение В-В.
Это сечение под зубчатым колесом. Концентрация напряжений обусловлена наличием шпоночной канавки.
Определяем коэффициент запаса прочности по касательным напряжениям.
Для этого находим:
Диаметр выходного конца вала d= 75 мм.
среднее напряжение отнулевого цикла Wк нетто=d3/16-bt1(d-t1)2/2d= 78278,71 мм3
амплитуда отнулевого цикла v=m=max/2=T2/2Wк нетто= 5,29 H/мм2.
принимаем по табл. 8.5. , 8.8 , эффективный коэффициент концентрации касательных напряжений k= 1,9
интерполируя, масштабный фактор для касательных напряжений = 0,64
коэффициент = 0,1
коэффициент, учитывающий влияние шероховатости поверхности = 0,95
Коэффициент запаса прочности s=-1/(k*v /(*)+*m)= 13,157
Определяем коэффициент запаса прочности по нормальным напряжениям .
Для этого находим:
Суммарный изгибающий момент берем из эпюр M= 495494 H*мм.
среднее напряжение отнулевого цикла Wк нетто=d3/32-bt1(d-t1)2/2d= 36861,23 мм3.
амплитуда отнулевого цикла v=m=max/2=T2/2Wк нетто= 22,48 H/мм2.
принимаем по табл. 8.5. , 8.8, эффективный коэффициент концентрации касательных напряжений k= 1,9
интерполируя, масштабный фактор для нормальных напряжений = 0,75
коэффициент = 0,2
коэффициент, учитывающий влияние шероховатости поверхности = 0,95
Коэффициент запаса прочности s=-1/(k*v /(*)+*m)= 6,005
Результирующий коэффициент запаса прочности для сечения В-В
s=s*s*/s2+s2= 5,463
Расчет на жесткость вала червяка.
Проверим стрелу прогиба для червяка. Для этого определим приведенный момент инерции поперечного сечения.
Jпр=d4f1/64*(0,375+0,625*da1/df1)= 719814,2752 мм4
Стрела прогиба f=l31* F2t1+F2r1/(48EJпр)= 1,37879E-07 мм.
Допускаемый прогиб [f]=(0,005...0,01)m= 0,05 0,1
Жесткость обеспечена, так как f<[f].
Тепловой расчет редуктора.
Температура воздуха tв= 20 ° С
Коэффициент теплопередачи Кt= 15 Вт/(м2*град)
Определяем по табл. 11.6 [1] площадь поверхности охлаждения в зависимости от межосевого расстояния А= 0,67 мм2
Температура масла без искусственного охлаждения при непрерывной работе tм=tв+Р1*(1-)/(Kt*A)= 74,3 ° С
Температура масла не превышает допустимой [t]м=80...95° С.
Z
X
Y
Рис.1 Эпюра моментов на быстроходном валу
Z
Рис.2 Эпюра моментов на тихоходном валу

Y
X
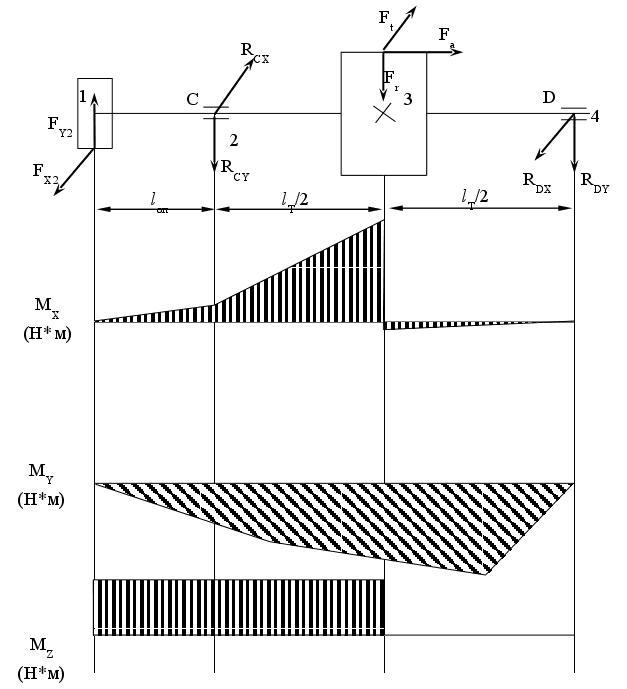
29-04-2015, 04:19