Министерство образования и науки Российской Федерации
Федеральное агентство по образованию
ИРКУТСКИЙ ГОСУДАРСТВЕННЫЙ ТЕХНИЧЕСКИЙ УНИВЕРСИТЕТ
Кафедра менеджмента на автомобильном транспорте
Допускаю к защите
Руководитель ___ __
И.О. Фамилия
ПОЯСНИТЕЛЬНАЯ ЗАПИСКА
к курсовой работе по дисциплине
«Основы логистики»
Выполнил студент группы _______
шифр подпись И.О. Фамилия
Нормоконтролер ________ ________ _ ___
подпись И.О. Фамилия
Курсовой проект защищен
с оценкой _______________
Иркутск 2010 г.
СОДЕРЖАНИЕ
Введение ………………………………………………………………………… 3
1 Выбор тары и упаковки, способа погрузки – разгрузки и погрузочно-разгрузочных механизмов ……………………………………………………… 5
2 Расчёт площади грузового склада …………………………………………….8
3 Выбор погрузочно-разгрузочных механизмов и расчёт
их количества ……………………………………………………………………..9
4 Расчёт числа автомобилей и количества ездок …………………………… ..11
5 Расчёт числа подач вагонов и длины фронта погрузочно-разгрузочных работ ……………………………………………………………………………. 16
6 Расчёт продолжительности обработки автомобилей и вагонов ………….. 17
7 Определение объёма прямой перевалки грузов …………………………… 19
8 Построение графика работы крупного склада …………………………….. 22
9 Оптимизация числа грузовых механизмов ………………………………… 23
10 Организационно – технологические мероприятия по повышению эффективности использования подвижного состава …………………………40
Заключение ………………………………………………………………………41
Список литературы ……………………………………………………………. 42
ВВЕДЕНИЕ
Повышение эффективности автомобильных перевозок грузов связано с техническим усовершенствованием подвижного состава автомобильного транспорта и погрузочно-разгрузочных средств, внедрением прогрессивной технологии совершенствованием организации перевозки грузов. Технические усовершенствования позволяют увеличить скорость движения подвижного состава, сократить простои под погрузочно-разгрузочными операциями, увеличить объем партии перевозимого груза и т.д. Задача технологии – сократить продолжительность и трудоемкость перевозки груза за счет уменьшения числа выполняемых операций и этапов процесса перевозки.
Под технологией процесса перевозки груза понимается способ реализации людьми конкретного перевозочного процесса путем расчленения его на систему последовательных взаимосвязанных этапов и операций, которые выполняются более или менее однозначно и имеют целью достижение высокой эффективности перевозок. Задача технологии – очистить процесс перевозки грузов от ненужных операций, сделать его целенаправленнее. Сущность технологии перевозки грузов выявляется через два основных понятия – этап и операция. Этап – это набор операций, с помощью которых осуществляется тот или иной процесс. Операция – однородная, логически неделимая часть процесса перевозки, направленная на достижение определенной цели, выполняемая одним или несколькими исполнителями.
Технологию любого процесса перевозки груза характеризуют три признака: расчленение процесса перевозки, координация и этапность, однозначность действий. Назначение расчленения процесса перевозки грузов на этапы представляет собой определение границ имманентных требований к субъекту, который будет работать по данной технологии. Любая операция должна обеспечивать приближение объекта управления к поставленной цели и обеспечивать переход от одной операции в другую. Последняя операция этапа должна быть своеобразным введением к первой операции следующего этапа. Чем точнее описание процесса перевозки грузов будет соответствовать его субъективной логике, тем большая вероятность достижения наивысшего эффекта деятельности людей, занятых в нем. Разрабатываемые технологии должны учитывать требования основных экономических законов и, в первую очередь, закона повышения производительности общественного труда.
Координация и поэтапность действий, направленных к достижению поставленной конкретной цели, должны базироваться на внутренней логике функционирования и развития определенного перевозочного процесса. Технология не создается на «пустом месте», а имеет связь с технологией прошлого и будущего. Технология, действующая сегодня, должна базироваться на принципах, которые позволяли бы легко переделывать ее в технологию будущего.
Каждая технология должна предусматривать однозначность выполнения включенных в нее этапов и операций. Отклонение выполнения одной операции отражается на всей технологической цепочке. Чем значительнее отклонение параметров от запроектированных технологией, тем больше опасность нарушить весь процесс перевозки груза и получить результат, не соответствующий проекту.
Вначале разрабатывается технология всего процесса перевозки грузов, а потом отдельных этапов. После разработки технологии этапов их необходимо рассмотреть с позиции технологического единства.
Между техникой и технологией существует причинно-следственная связь, однако решающее значение принадлежит технике.
Технологический процесс изобретен не сегодня. Подобно тому, как, по словам Мольера, люди не задумываются над тем, что пишут и говорят прозой, так и работники автотранспортных предприятий, используя определенную технологию, не задумываются над ней. В прошлом технологии процесса перевозки грузов формировались в большинстве случаев интуитивно. Технологические процессы перевозки грузов не были целенаправленно и сознательно разработанными системами этапов и операций. Поэтому в настоящее время очень многие перевозочные процессы недостаточно эффективны.
1 ВЫБОР ТАРЫ И УПАКОВКИ, СПОСОБА ПОГРУЗКИ – РАЗГРУЗКИ И ПОГРУЗОЧНО-РАЗГРУЗОЧНЫХ МЕХАНИЗМОВ
ГСМ – один из основных экономических и транспортных ресурсов нашей страны. Большое влияние на развитие химического комплекса оказывают пропускная способность транспортных коммуникаций и качество подготовки к перевозке.
В данном случае ГСМ перевозятся в бочках. Используем металлические бочки объемом 200 литров (ГОСТ – 13950 – 91, Бочки стальные сварные и закатные с гофрами на корпусе).
Для погрузки и разгрузки ГСМ в бачках выбираем поддон типа 2ПВ2-двухнастильный двухзаходный с выступами для обращения на автомобильном и железнодорожном транспорте размерами .
|
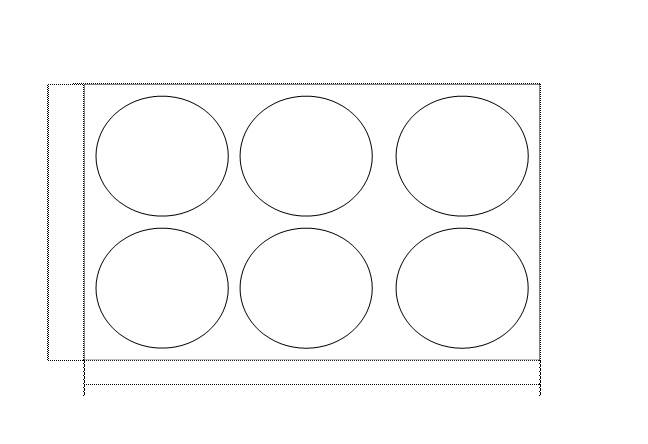
Рисунок 1.1 – Размещение ГСМ в бочках на поддоне типа 2ПВ2.
Выбор типа подвижного состава осуществляется в зависимости от вида перевозимого груза, объема перевозок, средней длины груженной едки, размера отправок и др.
Выбираем 2 автомобиля МАЗ – 53362 и МАЗ – 5429 с полуприцепом МАЗ 9392 и сравниваем их по производительности
МАЗ – 53362 |
|
Грузоподъёмность, |
8,28 |
Габаритные размеры кузова, Длина кузова Ширина кузова Высота борта |
6100 2420 695 |
МАЗ – 5429+п/п МАЗ 9392 |
|
Грузоподъёмность, |
20,9 |
Габаритные размеры кузова, Длина кузова Ширина кузова Высота борта |
11500 2500 650 |
, (4.2)
где грузоподъёмность автомобиля, т (конт.);
коэффициент использования грузоподъёмности;
техническая скорость движения автомобиля, км / ч.;
коэффициент использования пробега автомобиля;
среднее расстояние ездки с грузом, км.;
время погрузки – разгрузки автомобиля, ч.
, (4.3)
где количество поддонов, необходимое при погрузке одного автомобиля;
вес одного поддона с ГСМ в бочках,
.
mбочки
брутто
*Nб
*+mподдона
=169*6+115=1129кг
mподдона =115кг
mбочки =15кг
mбочки брутто = mбочки +mгсм =15+154=169кг
mгсм =V*ρ=0,2*770=154кг
Vб =0,2м3
ρбензина =770кг/м3
Производительность МАЗ – 5429+п/п МАЗ 9392
13550
13550 кг = 13,55 т.
0,65
0,65
0,8
0,8 ч.
8,6
8,6 т / ч.
Производительность МАЗ – 53362
6775
6775 кг = 6,775 т.
0,82
0,82
0,4
0,4 ч.
Выбираем МАЗ – 5429+п/п МАЗ 9392
Рисунок 1.3 – Размещение химикатов в бочках на автомобиле МАЗ – 5429+МАЗ 9392.
Автопогрузчики относятся к универсальным самоходным погрузочно-разгрузочным машинам. Благодаря высоким эксплуатационным качествам автопогрузчики получили широкое распространение в различных отраслях народного хозяйства, в том числе на транспорте, в строительной индустрии, промышленности. Автопогрузчики характеризуются высокой производительностью, мобильностью и способностью выполнять погрузочно-разгрузочные работы в различных эксплуатационных условиях с контейнерами и другими тяжеловесными грузами, со штучными грузами в пакетах, на поддонах, с длинномерными грузами и с сыпучими материалами. Для выполнения погрузочно-разгрузочных операций с разнообразными грузами автопогрузчики оборудуются быстросъемными грузозахватными устройствами: вилочным захватом, безблочной стрелой со стропами, ковшом и т.д. Поэтому для погрузки – разгрузки ГСМ в бочках выбираем автопогрузчики 4022 и 4013.
2 РАСЧЁТ ПЛОЩАДИ ГРУЗОВОГО СКЛАДА
Площадь грузового склада определяется по следующей формуле:
, м2
(2.1)
где срок хранения грузов на складе, сут.;
нагрузка на единицу площади склада, т / м2
;
коэффициент, учитывающий наличие на складе проходов и проездов,
1,8 – 2,0;
техническая норма загрузки вагонов, т.;
коэффициент прямой перевалки грузов из вагонов в автомобили и обратно, первоначально принимается равным 0.
16852
16852 м2
.
Среднеквадратическое отклонение находится по следующей формуле:
, (2.2)
где и
эмпирические коэффициенты для основных видов грузов;
среднесуточное количество вагонов, поступающих в пункт перевалки, ваг.
(2.3)
80,75
80,75
81 ваг.
1,289 * 17,55 = 22,622
23
Для хранения химикатов в бочках выбираем крытый склад без ввода путей вовнутрь.
Таблица 2.1 – Основные параметры крытого склада без ввода путей вовнутрь.
Вид склада |
Крытый склад без ввода путей вовнутрь |
Размер склада, м. |
|
Количество дверей со сторон автотранспорта |
3 |
Количество дверей со сторон железнодорожного транспорта. |
4 |
Вид грузов, для хранения которых предназначен. |
Огнеопасные грузы и химикаты |
Общая длина складов находится как
, (2.4)
где полезная ширина склада, м.
1123,5
1123,5 м.
Если общая длина складов превышает 400 – 500 метров, то целесообразно их разбить на две или три параллельные линии с таким расчётом, чтобы длина каждой линии не превышала 400 метров. В данной ситуации я разбиваю свой склад на 3 параллельные линии. Такая планировка позволяет сократить пробег автотранспорта и обеспечить более удобное размещение складов на территории перевалочного пункта.
3 ВЫБОР ПОГРУЗОЧНО-РАЗГРУЗОЧНЫХ МЕХАНИЗМОВ И РАСЧЁТ ИХ КОЛИЧЕСТВА
При обосновании способа погрузки – разгрузки и выборе соответствующих погрузочно-разгрузочных механизмов необходимо учитывать характер груза, тару и упаковку, тип склада или площадки. При этом следует проанализировать различные способы погрузки – разгрузки, разные виды грузовых механизмов (козловой кран и автокран, автокран и автопогрузчик и т.п.).
Выбор рационального вида грузового механизма производится по его часовой производительности:
, (3.1)
где 3600 – перевод часов в секунды;
фактическая грузоподъёмность грузового механизма, т (конт.);
время цикла, сек.
Время цикла для электропогрузчиков рассчитывается по следующей формуле:
, (3.2)
где время захвата – установки груза, сек;
время перемещения груженого и порожнего автопогрузчика, сек.
Время цикла для автопогрузчика 4022:
213
213 сек.
Время цикла для автопогрузчика 4013:
180
180 сек.
Время перемещения гружёного и порожнего автопогрузчика 4022:
(3.3)
153
153 сек.
Время перемещения гружёного и порожнего автопогрузчика 4013:
(3.4)
120
120 сек.
Часовая производительность автопогрузчика 4022:
19,1
19,1 т / ч.
Часовая производительность автопогрузчика 4013:
22,6
22,6 т / ч.
После выбора вида грузового механизма рассчитывается его годовая производительность:
, (3.5)
где дни работы грузового механизма в течение года, сут.;
дни нахождения грузового механизма в ремонте, сут.;
продолжительность работ механизма в течение суток,
ч.;
коэффициент использования грузового механизма по времени,
.
Годовая производительность автопогрузчика 4013:
147532,8
147532,8 т / ч.
Расчёт количества грузовых механизмов, необходимых для разгрузки поступающего грузопотока, производится по формуле:
, (3.6)
где годовой объём поступления грузов, т (конт.);
коэффициент неравномерности поступления грузов в течение года,
.
Расчёт количества автопогрузчика 4013, необходимых для разгрузки поступающего грузопотока:
10
10 ед.
Общее количество грузовых механизмов определяется по формуле:
(3.7)
Общее количество автопогрузчиков 4013:
20 ед.
Часовая и годовая производительности автопогрузчика 4013 больше часовой и годовой производительности автопогрузчика 4022. Таким образом для погрузки ГСМ в бочках выбираем автопогрузчик 4013.
4 РАСЧЁТ ЧИСЛА АВТОМОБИЛЕЙ И КОЛИЧЕСТВА ЕЗДОК
Число автомобилей для обслуживания перевалочного пункта рассчитывается по формуле:
, (4.1)
где потребное число автомобилей, ед.;
дни работы автомобилей в течение года, сут.;
продолжительность работы автомобилей в течение суток, ч.;
часовая производительность одного автомобиля, рассчитываемая по формуле
52
52 ед.
Далее рассчитывается количество автомобилей, приходящихся на один погрузочно-разгрузочный механизм:
(4.4)
3
3 ед.
Затем рассчитывается общее количество ездок автомобилей, необходимых для вывоза грузов из перевалочного пункта:
, (4.5)
где количество груза, ввозимого автомобилями в течение суток, т.
329
329 ездок.
(4.6)
4457
4457 т.
И количество ездок автомобилей, приходящихся на один погрузочно-разгрузочный механизм:
(4.7)
17
17 ездок.
Количество ездок автомобилей, приходящихся в
29-04-2015, 02:49